Rolling Floors
This is an excerpt from the Book called “Home Repair and Improvement Series” by Bob Vila. Continue reading to learn more about Rolling Floors, thanks to the author.
Rolled Flooring: Seamless And Easy On The Feet
Years ago, rolled sheets of flooring were made of only one material—linoleum. Today the material is almost certain to be sheet vinyl—easy to maintain and install.
Sheet vinyl comes in two basic types: inlaid, in which the pattern is pressed through the vinyl; and rotogravure or “roto’’ for short, in which the pattern is printed on the surface. both come in compositions of differing resiliency, some so flexible you can roll them into a ball and others so brittle they split if you try to press them into a corner.
Of the two types roto offers a greater variety of colors and patterns. It is softer and more soundproof; its wear surface is thin and the vinyl sheet has a thick foam-rubber backing called fatback. It is available in 6-, 12- and occasionally 9-and 15-foot widths—an advantage, because the variety of widths virtually
Eliminates the need for seaming, the most difficult part of laying sheet vinyl. But roto’s softness makes it easier to puncture, and some furniture—a kitchen table, for instance—can leave a permanent indentation if left too long in one spot. Inlaid sheet vinyl is harder and more durable, but usually comes only in 6-foot rolls.
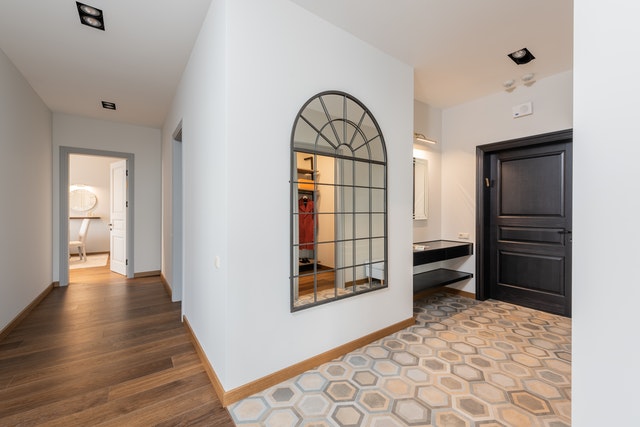
As the first step in an installation make a plan of the floor, marking the dimensions. Add 6 inches at each wall for overlap and note the width of the pattern repetition, usually printed on the back of the sheet, if you must seam sheets together. The allowance for seaming equals this width; for example, if your pattern repeats ever 3 feet, allow 3 feet of extra width when you buy the material.
Remove the shoe molding and generally the baseboard, too; it is best replaced with cove molding remove all the old wax and sweep the floor clean.
When returning heavy appliances, such as the refrigerator, to the room after the vinyl has been laid, push them back on top of a sheet of hardboard to avoid making deep, permanent ridges in the vinyl.
Leave the fitting of the vinyl to a thresh old for the final step of the job. At an existing marble of wood threshold, cut the vinyl as close to the threshold as possible, shaving a little at a time to arrive at a close fit. If there is no threshold, of if you are planning to replace it, use metal edging strips, which is the best transition from new vinyl flooring to the floor covering in an adjoining room. If you use a metal tuck-in strip as a threshold leave the vinyl edge in the doorway unglued until the strip is installed.
- Rolling Out The Material.
Let the material adjust to room temperature for an hour or so; then, if you are using more than one sheet of material, start unrolling the larger sheet from the longest and most nearly clear wall of the room. Leave 3 to 6 inches of overlap at each wall.
When you reach a large immovable object, such as a center island of a set of built-in cabinets, reach under the roll and unroll the sheet back-ward toward the starting wall. Push the unrolled section of the sheet against the object and, about 6 inches above the floor, cut the sheet from its outside edge toward its center with a utility knife. Continue the cut about 6 inches short of the edge of the object, Then cut back toward the starting wall for a distance at least 6 inches less than the object’s depth.
- Fitting Around A Large Object.
Lift the roll over the object and lower it to the floor on the other side. holding the corner of the flap you have made in the sheet, complete the cutout for th object by cutting, if necessary, to a point about 6 inches from its far edge, then cutting at a right angle toward the outside edge of the sheet.
- Fitting around a small object.
Roll the material past a pipe or other small obstruction and slice a slit from the nearest edge of the material to the object. Carefully carve a circle around the object, making several cuts if necessary, then press the sheet together behind the object. if the slit is long, seal the seam for a neat job, slide the base ring up the pipe before laying the vinyl, then return it to the finished floor; if the pipe does not have a base ring, use the model shown here, which snaps around the pipe and screws to the floor.
- Reversing The Roll.
Unroll the sheet completely, pull it back upon itself and reroll the sheet back from the far edge with the underside of the sheet inside the roll. (The tight original roll in this area compresses the pattern, unless the roll is reversed briefly, the pattern will be smaller in one part of the room than the other.) Unroll the sheet again and press the material into all corners, to the extent that its natural resiliency will allow. Caution: do not try to force brittle material into a corner; it will split if pressed too tightly.
- Laying the second sheet.
Measure the width of uncovered floor from the edge of the first sheet to the wall: To this distance add 6 inches plus the amount of overlap required to match the floor-covering pattern. Mark the total distance on the second sheet and cut off any excess material.
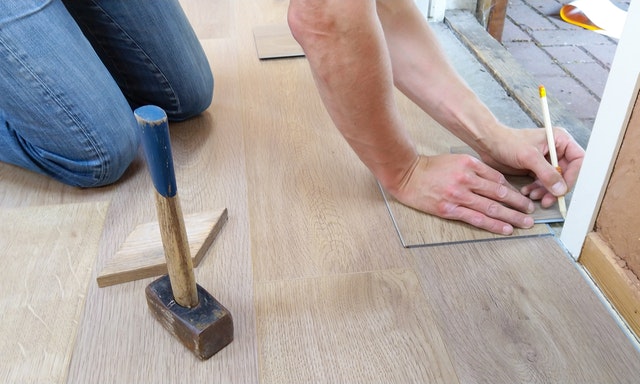
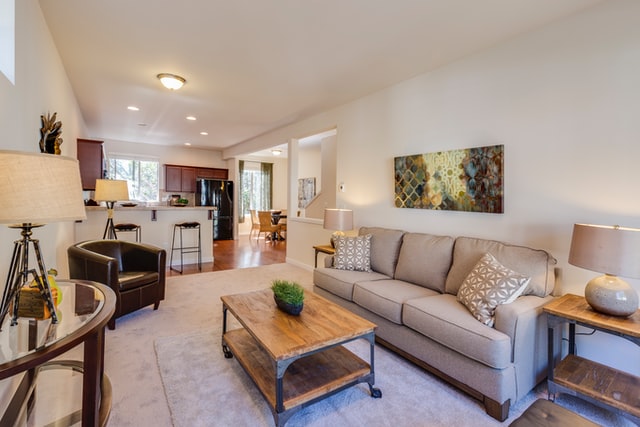
Roll the second sheet out halfway. Then pull it over the first sheet until the patterns march. Unroll the rest of the second sheet as you did the first, cutting around objects.
- Trimming The Edges.
Pull the second sheet off the first and out of the way. At each wall and object, cut the material back to about 3 inches above the floor. Caution: for professional-looking results, take care in making this cut—you are now close to the final trim.
- Applying The Adhesive.
Pull the first sheet halfway back upon itself. Using a trowel with 1\16-inch grooves, spread adhesive over the floor; do not cover a 6-inch strip along the line at which the first sheet will meet the second, but work the adhesive into corners as closely as possible. Follow the manufacture’s recommendations for the choice of an adhesive and any instructions on its use; the guarantee may depend upon strict adherence to this advice.
At the completion of this step, go on to the next immediately: after about 45 minutes most adhesives become so stiff that the material is hard to adjust.
- Setting The Vinyl In Place.
Lift the edge of the rolled material high above the floor and slowly walk it back into place over the adhesive. Lay it against the wall and press it into place at the corners as closely as its resiliency will allow.
- Rolling Out The Bumps.
Using an ordinary rolling pin or a rented tile roller, and starting from the center, roll the material toward each of its edges. Work slowly, and be sure to flatten any bulges or air bubbles that have risen above the flat surface.
- Making The Final Cuts.
Press a metal yardstick hard along the lines where walls or objects meet the floor, creasing the material sharply at the corners, then slice the material at the wall along the edge of the yardstick with a utility knife. You may not be able to crease inlaid sheet vinyl sharply at a first try; instead, make repeated cuts until the vinyl fits the corner. Caution: Normally, molding will cover cutting errors to about 1\2 inch from the wall, but ceramic cove; molding is not removed before laying the vinyl; for this type of molding the cuts must be exact.
- Cutting Of The Trim.
Place a metal yardstick along the overlapping edge of the second vinyl sheet and cut off the 1\2-to 1-inch trim at the edge of the sheet. On inlaid vinyl this trim is likely to be an extra-wide grout line: cut along the line to bring its width down to that of the other grout lines in the pattern.
- Matching The Pattern.
Pull the second sheet over the first until the patterns of the two sheets match perfectly. Caution; note the pattern carefully to be sure the overlap continues the pattern in the same manner—a mismatched pattern will spoil the appearance; of the finished job.
- Cutting Off The Overlap.
Place a metal yardstick along the edge of the top sheet and, holding a utility knife straight up and down and using the yardstick as a guide, cut through the bottom sheet. Pull the top sheet back and remove the strip you have cut from the bottom.
If the material you are using is resilient enough to permit a cut through two sheets at once, overlap the second sheet to a segment of pattern repetition and, using a yardstick as a guide, cut through both sheets at once. This method assures a perfect match of the pattern.
Lay the second sheet as you did the first, cutting overlaps of 3 to 6 inches around objects, spreading the adhesive to within 6 inches of the edge of the first sheet and making a final t4rim along each wall and object.
- Applying Adhesive Under The Seam.
Check the manufacturer’s directions for sealing the seam between two sheets if they do not call for seam sealer below the sheets. Simply pull back the butted edges on both sheets and spread adhesive over the bare floor along the entire length of the seam, then. While the adhesive is still plastic. Push the sheets back into place. Pressing the edges together until you get a tight fit. Go on immediately to the next step.
- Sealing The Seam.
Press the seam together with the thumb and finders of other. Most seam sealers are applied with a t-shaped nozzle (inset) with the top of the t riding on top of the material and the bottom inside the seam. Caution: some manufactures require that sealing be applied beneath the seam—consult the manufacture’s directions for sealing before carrying out step 14, above. For either method, wiped away all excess sealing immediately and do not step on the seam for at least 24 hours.